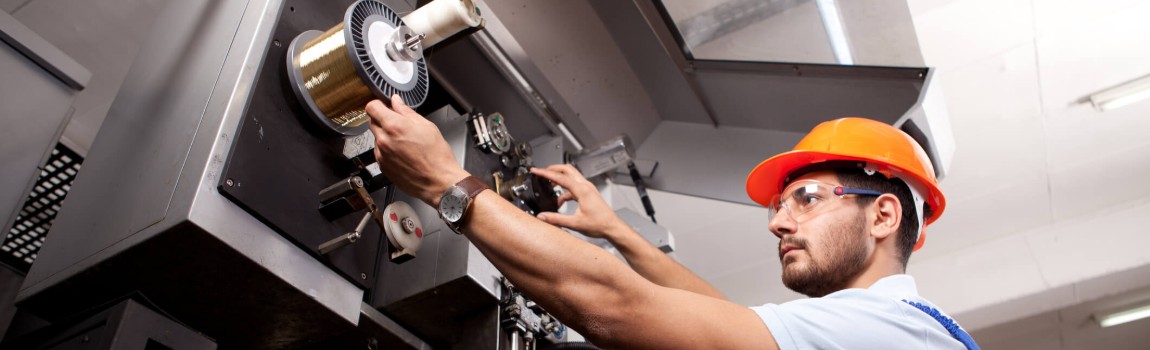
A gestão de manutenção industrial tem se tornado uma atividade cada vez mais importante nas organizações. O desgaste é um processo evidente ao longo do ciclo de vida dos maquinários, portanto, é fundamental realizar uma boa administração dos serviços para que os equipamentos tenham a duração necessária.
A constância das atividades em uma realidade cada vez mais digitalizada e globalizada torna essencial o acompanhamento minucioso de todos os processos. Uma manutenção industrial eficaz é o primeiro passo para a gestão eficiente dos gastos, conquistando uma inteligência estratégica mais assertiva.
Pensando nisso, desenvolvemos este artigo para apresentar mais informações sobre o processo de gestão de manutenção industrial e a sua importância para o setor. Acompanhe!
O que é gestão de manutenção industrial?
A gestão de manutenção industrial consiste no processo de supervisão do funcionamento adequado de todos os recursos técnicos dentro de uma organização. Além do controle dos ativos permanentes, como é o caso dos equipamentos, ferramentas e instalações, essa inspeção evita paradas de produção e desperdícios de montantes de dinheiro.
Geralmente, as paradas de produção são causadas pela quebra ou ociosidade dos equipamentos, que deixam de ser utilizados pela falta de manutenção adequada. Dessa forma, o processo de assistência ineficiente resulta no aumento dos gastos, encarecendo o processo produtivo.
Sendo assim, os principais objetivos do gerenciamento de manutenção envolvem a programação eficiente das rotinas de trabalho, o controle de custos e a garantia de qualidade no processo produtivo. O uso de softwares de gestão pode auxiliar nessa atividade.
Qual a importância da gestão de manutenção industrial?
Ao longo do processo produtivo, cada vez mais é necessário que os gestores estejam atentos à manutenção industrial, que reflete diretamente na qualidade de seus serviços. Ter sempre à disposição todos os equipamentos garante confiabilidade ao sistema, não permitindo que paradas não-programadas prejudiquem a dinâmica da empresa.
Dessa forma, a gestão de manutenção industrial assegura que todo o processo de assistência nos componentes da organização esteja sempre em funcionamento adequado, aumentando a eficiência e criando um plano para a redução dos custos por unidade. Toda essa dinâmica é pensada levando em consideração o aumento da qualidade e a garantia de bem-estar dos colaboradores.
Sobretudo, essa gestão deve ser encarada como um investimento, devendo ser uma parcela da decisão estratégica por parte dos administradores. O aumento da satisfação dos clientes eleva o número de vendas, refletindo diretamente na lucratividade. No entanto, toda essa situação só é alcançada com o acréscimo de produtividade sem perda da qualidade.
Quais são os principais modelos de manutenção?
A gestão de manutenção de ativos é dividia em duas categorias principais: as planejadas e as não-planejadas. Cada uma delas têm subdivisões de acordo com suas características. Pensando nisso, apresentamos os principais grupos e como esses modelos impactam na administração de assistências. Confira!
Manutenção planejada preventiva
A manutenção planejada preventiva reflete na necessidade de reduzir e evitar falhas, antevendo quedas na produção e no desempenho dos equipamentos. Geralmente, essa categoria envolve tarefas sistemáticas de inspeção, substituição de componentes e reformas.
Assim, a manutenção preventiva atua no monitoramento do desgaste natural, de maneira constante e fundamental para as empresas. Esse serviço preza pela eficiência e organização, agendando supervisões e trocas nos maquinários para que o processo produtivo não seja interrompido.
Manutenção planejada preditiva
Essa categoria de manutenção faz uso de dados e instrumentos específicos para compor os indicadores de desempenho de um equipamento. No geral, são levantadas informações como temperatura, análises físicas e químicas, vibrações, entre outros aspectos, que contribuem para um diagnóstico completo do maquinário.
Esses dados ajudam na prevenção da deterioração, prevendo possíveis problemas que interrompam o funcionamento do equipamento. Esse processo de manutenção preditiva é específico e feito em momento adequado, evitando que surjam consequências mais sérias.
Manutenção planejada corretiva
Por ser um processo esperado, essa categoria planeja os recursos necessários que serão utilizados no procedimento de assistência. Os principais aspectos que afetam na decisão do uso de manutenção planejada corretiva são:
- paradas programadas na produção, de acordo com o planejamento da equipe;
- segurança dos equipamentos e dos colaboradores;
- execução de melhorias na produtividade e no planejamento dos serviços;
- terceirização do serviço de manutenção por parte da administração.
Manutenção não-planejada corretiva
A manutenção não-planejada corretiva surge de maneira aleatória e inesperada, devendo corrigir imediatamente as adversidades, com o objetivo de evitar maiores problemas. Em questão de custos de assistência, representa a maior despesa do setor. Além disso, dependendo de onde foi identificada a falha, a produção pode ser interrompida, prejudicando a imagem da empresa e aumentando o prejuízo.
Qual a relação da gestão de manutenção industrial com a indústria 4.0?
A indústria 4.0 está relacionada com a revolução proporcionada pela internet das coisas, caracterizada pelos grandes avanços tecnológicos e de informação ao longo de todo o ciclo produtivo. Essa dinâmica possibilita o compartilhamento de dados com mais eficiência e em tempo real, com a comunicação direta entre os seres humanos e as máquinas.
Dessa forma, o setor de gestão de manutenção industrial tem sido impactado pela indústria 4.0, facilitando os processos de gerenciamento dos sistemas de produção, dando mais capacidade de planejamento e operação. Desse modo, as decisões podem ser tomadas de forma autônoma, fazendo com que as empresas prevejam falhas e agendem assistências com maior capacidade.
O monitoramento dos equipamentos em tempo real aumentou o controle por parte das indústrias, evitando que o processo produtivo fique ocioso por longos períodos devido às ações corretivas imediatas. Da mesma forma, essa dinâmica trouxe a aplicação mais direta de manutenção preventiva, antecipando os futuros problemas.
Assim, a partir da internet das coisas, os maquinários estão munidos de sensores e atuadores, programados para difundir as informações pertinentes e tomar as decisões por conta própria. Algumas das principais vantagens desse mecanismo são:
- diminuição do número de horas extras;
- aumento da produtividade;
- redução dos custos com materiais e estoques;
- aumento do tempo de disponibilidade dos ativos;
- redução dos custos de manutenção;
- diminuição dos impactos ambientais.
Quais são as principais vantagens da gestão de manutenção industrial?
Todos os procedimentos realizados precisam ser compreendidos na sua totalidade para que objetivos claros sejam definidos. A teoria de gestão de manutenção não é difícil, mas conhecer adequadamente sua importância é fundamental para as ações da empresa. Para isso, separamos algumas das principais vantagens dessa atividade para as organizações. Descubra!
Eficiência no trabalho
Um programa de manutenção mal otimizado não evita que interrupções constantes ocorram na organização. Muitas vezes, as equipes de assistência estão atuando na resolução de problemas de equipamentos que não são essenciais ao processo produtivo, enquanto outros maquinários estão ociosos.
Por isso, é necessário que o gerente de manutenção entenda todos os processos da empresa, realizando agendamento e controle. Organizar a quantidade de colaboradores por equipe de acordo com as atividades e armazenar adequadamente os produtos são ações muito positivas nessa dinâmica.
Agendamento de tarefas
Outro fator importante é a ordem de prioridade para diferentes equipamentos no processo produtivo. Diversos aparelhos podem necessitar de manutenção ao mesmo tempo, mas os que devem ser reparados primeiro são os essenciais ao ciclo de produção. É papel do gerente conhecer toda a dinâmica da empresa e adequar seus planos de assistência.
Controle de custos
A partir de um orçamento específico do departamento de manutenção, o gerente tem a responsabilidade de atuar com as ferramentas que lhe são oferecidas. Sendo assim, análises constantes de custo-benefício devem ser realizadas, sempre em prol dos processos produtivos essenciais.
Conformidade com as leis
Por fim, um aspecto muito importante é a garantia de realização das tarefas em conformidade com as leis e regulamentações locais, estaduais e federais. Um exemplo prático dessa situação é o número de funcionários mínimo para determinada atividade, devendo seguir as instruções de segurança para evitar multas.
Sobretudo, a gestão de manutenção industrial é uma atividade fundamental dentro das organizações. Esse processo garante que todo o ciclo produtivo seja mais eficiente e que os custos sejam reduzidos. Esse setor tem sido influenciado pela indústria 4.0, com o monitoramento dos equipamentos em tempo real. A eficiência no trabalho e a conformidade com as leis são algumas das vantagens dessa administração.
Gostou deste artigo? Então continue com a visita em nosso blog e descubra como a Dimensional acompanhará a revolução da Indústria 4.0!
[rock-convert-cta id=”227″]